
Eco-material World
April 15, 2015
My mud slinging days were only beginning with the completion of the earthen stove at Pedregál. Since then, I’ve sought out other opportunities for sinking my toes in mud, including a very full 3-day workshop in Nochixtlán entitled Volver a la Tierra (Return to the Earth). Projects included constructions such as tapia pisada (rammed earth), bahareque (wattle and daub walls), carrizo (cane) arches, lime wash paint, an adobe brick vault and an adobe brick oven. With an attendance of up to 300 people simultaneously working with the earth, it really felt like a bustling ant farm — me a very contented, wide-eyed drone.

I’ve found a true calling with these natural building methods. After all, they fit many of my keenest interests: earth-loving low impact sustainable architecture, outdoor hippy activities of intimacy with the natural environment and economic egalitarian off-the-grid ways of providing for one’s self. After the workshop I sought out more opportunities like this, and found Eco Constructores Oaxaca. This is a mission-oriented organization that provides alternative building services — using natural materials — to communities and private clients.
Eco Constructores aims to proliferate the use of building with natural materials by making these services available to a wide spectrum of people whilst educating as many people as possible in the methods. They have an admirable economy of labor in place where in addition to having paid staff constructing the projects, they invite any curious volunteer to participate as well. The staff is very accustomed to having new volunteers all the time, and is incredibly patient and enthusiastic about teaching. Since they are constantly interrupted by having to pause to teach something – or save something from being ruined – the work goes much slower. But they do receive in return a little bit of free, inefficient labor from the volunteers, and that all might just even out in the end.

I’ve been spending a good deal of time participating at a site just outside Oaxaca City, just outside the town center of Guadalupe Etla. The project is a private house of adobe and bahareque. The 3 exterior adobe brick walls were existing on site with a roof that will be replaced, supported by fired brick columns; the former building served as a bodega, or large multi-purpose storage shed. To convert the bodega into a habitable house, they are completing another exterior wall and adding interior partition walls, as well as replacing the roof, adding a bathroom and kitchen, and finishing the floors.
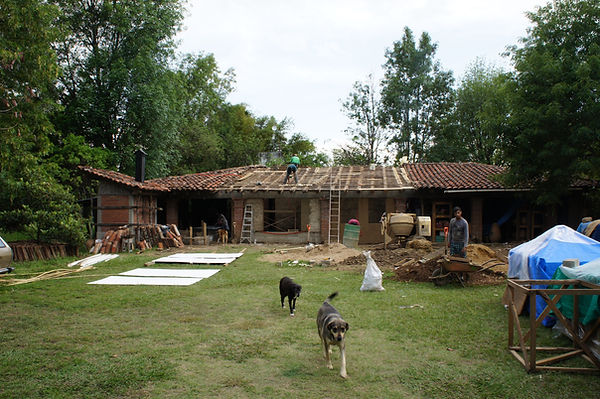

Over the past few months, I’ve been learning the most about the construction of bahareque walls. This is partially due to the fact that these walls take an extremely long amount of time to construct in comparison to the stick-framed-sheetrock-clad walls I’m used to seeing in the US. Coined elsewhere in Latina America, bahareque is an ancient type of wattle and daub wall, which have been used around the globe for at least the past 6,000 years.
Aside from being relatively earthquake resistant, bahareque construction has the advantage of local material sourced sustainability here in Oaxaca. That is, not only is off gassing greatly reduced by using drying mud (rather than something like concrete), but it is very probable that you can source all your building materials directly on site, making a very low carbon footprint. When constructing a bahareque wall, you are essentially making a giant adobe brick, custom sized and installed to form a wall. The general idea is straightforward: build a frame out of wood or reed material and fill it and cover it with a good mud mixture (similar to the mud stove in Pedgral: a mixture of dirt, sand, straw, and water).
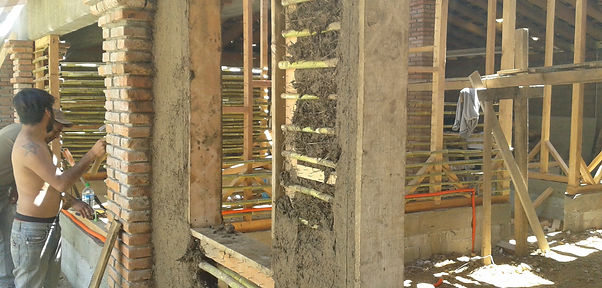
Filling the frames with the mud mixture is no small task. It’s time consuming and arduous, requiring a tremendous amount of weighty material. Making the frames relleno (like a chile relleno!) with mud is rewarded with the task of covering the filled frames, which is best done by the grin-inducing method of throwing handfuls of mud. Yes, more mud throwing! Really, the best way to get the right density and for the mud mixture to stick well is to throw mud patty after mud patty at the wall to slowly build up the layers.
Once layers of mud wads are built up, a wet hand does the trick to roughly smooth it over to plane it a bit. This is a very similar method to one I use when making gingerbread; gingerbread dough is very sticky, and to get it even in the pan so it bakes evenly, the trick is to wet your hand first and manually smooth it over.

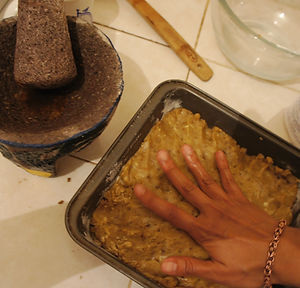
I made the link between gingerbread and bahareque while baking some gingerbread the other day to bring out to the site. Working hard all morning, everyone looks forward to the picnic break at one o’clock, where everyone brings something to share and someone often makes carne asada (barbecue). I haven’t figured out a Spanish word for “picnic” yet (everyone keeps calling it simply comida, or “meal”), but I’ve been bringing my own meaning to it by making American dishes like potato salad and gingerbread.

Or, I should say, I’ve been making a variation on gingerbread, using piloncillo instead of molasses. Piloncillo (called panela in other parts of Latin America) is solidified unrefined cane sugar, different from brown sugar because it is unrefined. It has an earthy flavor kind of like brown sugar, but unlike brown sugar is unprocessed and also contains many minerals brown sugar lacks. I’ve been trying to use it when I would have used molasses in a recipe, since the only molasses I’ve seen here was in a bucket at the animal feed store where we purchased straw for the bahareque walls. Everything there was intended to feed livestock, rather than baking treats or building houses.

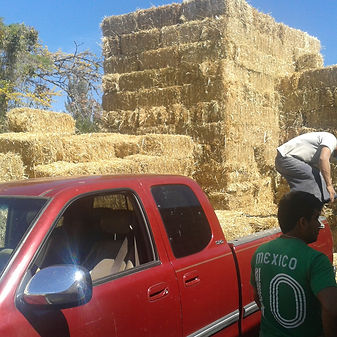
There aren’t any grasses (and therefore no straw) on site, so the straw has to be purchased for this particular project. However, something the site is rich in is carrizo. Carrizo is a reed that grows prolifically at the edges of rivers and streams, quickly renewing itself and sprouting new stocks where others have been harvested—essentially a Mexican bamboo. Carrizo is used to construct the frame which to fill with mud for the bahareque.
As much as I love throwing mud, I have thoroughly enjoyed the days I’ve spent harvesting and trimming the carrizo. The reeds we use are about twenty feet tall, so harvesting them involves moving through a reed forest like a tropical explorer, and then bending and jumping on the reeds to pop them out of the ground. Then, trimming involves using a machete in a similar motion as peeling carrots: a nice, rhythmic way to pass time in the shade on a hot day.
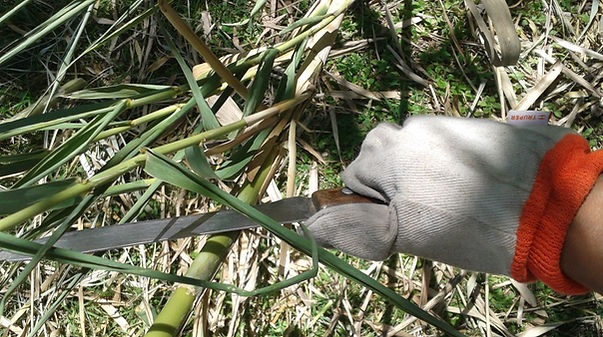
Very durable, easy to cut, and somewhat flexible, carrizo has many other uses besides construction. Ubiquitous in Oaxaca are woven baskets of carrizo in varying shapes and sizes, a sturdy reusable substitute to a cardboard box or plastic bin. Walking through Guadalupe Etla one day, some of the other workers and I met a 72 year old man weaving beautiful bread baskets out of carrizo. He also happened to live in a modest house of bahareque that had been standing since before he moved in 10 years ago.


Carrizo is also useful for another important construction activity: mezcal breaks. The reeds are jointed so that they may easily be sawed into nice little shot glasses. Nailing is hard. Mud is heavy to haul. Breaks are well deserved.

This house in Guadalupe Etla is still in progress, and much more work and many more natural building methods are to come. None of the bahareque walls have yet been finished, nor the floors nor the roof, so there’s great promise for many more mud pies and many more mezcal toasts. As they say, when it comes to mezcal, “one is not enough, two is almost enough, and three is one.”
